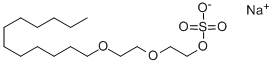
Sodium Laureth Sulfate synthesis
- Product Name:Sodium Laureth Sulfate
- CAS Number:3088-31-1
- Molecular formula:C16H33NaO6S
- Molecular Weight:376.48

3055-93-4
64 suppliers
$431.00/5g
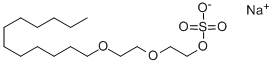
3088-31-1
44 suppliers
inquiry
Yield:-
Reaction Conditions:
Stage #1:diethylene glycol monododecyl ether with sulfur trioxide at 35 - 130;Industry scale;
Stage #2: with sodium hydroxide;sodium carbonate in waterProduct distribution / selectivity;Industry scale;
Steps:
1; 1; 4; 4
Comparison Example 1Preparation of Laureth (2EO) Sulfate, Sodium Salt in an Annular-Gap Falling-Film Reactor According to Conventional MethodsIn a conventional annular-gap falling-film reactor with a diameter of 5 inches and a reactor length of approximately 2 m with an annular gap width (annular space) of 6.5 mm and with one raw material distributor slit each on the inner wall of the outer tube and on the outer wall of the inner tube and each with a cooling mantle (see FIG. 2), a C12/14 fatty alcohol ethoxylate (fatty alcohol C12 content 70-75%, C14 content 25-30%, molecular weight 194 with 2 moles of ethylene oxide (molecular weight 282, APHA color number Hazen=14) was applied uniformly onto the two annular gap surfaces through the two distributor slits in an amount of 259 kg/h (mass flow meter) (=0.920 kmol/h of fatty alcohol ethoxylate) at a temperature of 40° C. The cooling water feed temperature was adjusted to 15° C. on both cooling mantles. The diluted SO3 was produced by combustion of sulfur to SO2 and subsequent oxidation to SO3.Using a feed tube, 0.888 kμmol/h of dilute SO3 gas (SO3/raw material=0.965) was introduced into the annular gap at a concentration of approximately 3.490 volume %. After degassing in a cyclone and cooling in a heat exchanger, the reaction mixture was brought to the lower part of the reactor for rapid cooling (quenching) of the hot reaction mixture. Temperature measurements in the annular gap showed that a temperature maximum of 130° C. occurred at approximately 115 mm from the feed of the fatty alcohol ethoxylate. The exit temperature at the end of the annular gap before quenching was 40° C. The degassed sulfonic acid which was removed from the reactor continuously was neutralized with sodium hydroxide (18 weight %), demineralized water, and sodium carbonate as buffer in a special dynamic mixer so that an approximately 70% paste was obtained. The product showed the following data:; After 5 days of running, the reactor had to be opened and cleaned because the color of the product was worsening. At the reactor head, directly where the liquid raw material and SO3 met, black crusting was observed which had to be washed off with dilute sodium hydroxide. The entire sulfation installation had to be shut down for 6 hours for this purpose.; Example 1Preparation of Laureth (2EO) Sulfate, Sodium Salt in an Annular-Gap Falling-Film Reactor According to the InventionIn the embodiment of an annular-gap falling-film reactor according to FIG. 5, a thin-walled (approx. 0.5 mm) double tube (3) having an outside diameter 124.1 mm, inside diameter 116.9 mm, and gap of 2.6 mm was built centered into the annular gap (annular space) (2). The overall tube distance (wall thickness plus gap) was 3.6 mm and the length was 330 mm. The diameter of the reactor (inside diameter of the outer tube(1)) was 5 inches (127 mm) with a reactor length of 1650 mm, with an annular gap (2) width of 6.5 mm, each having a raw material (4) distributor slit (5) on the inner wall (6) of the outer tube (1) and on the outer wall (7) of the inner tube (1) and each with a cooling mantle (14) (see FIG. 5). The diameter of the inner double tube (3) was dimensioned so that the SO3 gas was introduced in an amount of 50% through the annular gap (2) in the upper reaction zone (10) and 50% through the double tube (3).A feed (4) comprising a C12/14 fatty alcohol ethoxylate (fatty alcohol C12 content 70-75%, C14 content 25-30%, molecular weight 194) with 2 mol of ethylene oxide (molecular weight 282, APHA color number=14) were introduced through the two distributor slits (5) in an amount of 259 kg/h (mass flow meter) (=0.920 kmol/h of fatty alcohol ethoxylate) at a temperature of 40° C. uniformly onto the two annular gap surfaces (6) and (7). The cooling water (12) feed temperature on the two cooling mantles (14) was adjusted to 15° C. The dilute SO3 (8) was produced by combustion of sulfur to SO2 and subsequent oxidation to SO3. Using a feed tube (3), 0.888 kmol/h of dilute SO3 gas was introduced through the reactor head (9) into the annular gap (2) at a concentration of 3.490 volume %. After degassing in a cyclone and cooling in a heat exchanger, the hot reaction mixture was introduced into the lower part of the reactor for rapid cooling (quenching).Temperature measurements in the annular gap showed that a first temperature maximum of 60° C. occurred at 120 mm from the feed of the fatty alcohol ethoxylate. A second temperature peak at a temperature of 55° C. occurred at approximately 450 mm. The exit temperature at the end of the annular gap before quenching was 35° C. The degassed sulfonic acid was removed continuously from the reactor and was neutralized as in the comparison experiment with sodium hydroxide (18 weight %), demineralized water, and sodium carbonate as buffer in a special dynamic mixer so that an approximately 70% paste was produced. The product has the following data:; After 4 weeks of running, the reactor was opened. No crusting was observed at the reactor head directly where the liquid raw material and SO3 meet. The color of the product from the running production had not worsened either. The installation would not have had to have been shut down.; Comparison Example 4Preparation of Laureth (2EO) Sulfate, Sodium Salt in a Single-Tube Falling-Film Reactor According to the Conventional MethodIn a single-tube falling-film reactor (analogous to BALLESTRA) the organic material was applied uniformly as a film (see FIG. 4) through a special raw material feed system to the inner surface of the tube (1 inch=25.4 mm inside diameter, 8 m long, mantle cooling with two sections) (see FIG. 4). For the experiment a C12/14 fatty alcohol ethoxylate (C12 content 70-75%, C14 content 25-30%, molecular weight 238) with 2 mol of ethylene oxide (molecular weight 282, APHA number=10) was uniformly applied through a distributor slit in an amount of 21 kg/h (mass flow meter) (=0.077 kmol/h of fatty alcohol ethoxylate) at a temperature of 40° C., to the inner wall of the reaction tube. The cooling water feed temperature on the cooling mantle was adjusted to 15° C. The dilute SO3 was produced by combustion of sulfur to SO2 and subsequent oxidation to SO3. Using a feed tube, 0.074 kmol/h of dilute SO3 gas was introduced into the reaction chamber at a concentration of 3.420 volume %. At the end of the reactor at a length of approximately 10 m the sulfo acid is degassed through a cyclone.Temperature measurements in the reaction tube showed that a maximum temperature of 120° C. occurred at 400 mm from the fatty acid ethoxylate feed. The exit temperature at the end of the reaction tube was 40° C. The degassed sulfo acid removed continuously from the reactor was neutralized with sodium hydroxide (18 weight %), deionized water and sodium carbonate as buffer in a special dynamic mixer in such a way that a 70% paste was produced. The product has the following data:; After 5 days of running, the reactor had to be opened and cleaned because the color of the product was worsening. At the reactor feed, directly where the liquid raw material and SO3 meet, black crusting was observed which had to be washed off with dilute sodium hydroxide.; Example 4Preparation of Laureth (2EO) Sulfate, Sodium Salt in a Single-Tube Falling-Film Reactor According to the InventionIn a single-tube falling-film reactor (analogous to BALLESTRA), the organic raw material was applied uniformly, as a film through a special raw material feed system to the inner surface of the tube (1 inch=25.4 mm inside diameter, 8 m long, mantle cooling with two sections) (see FIG. 6). For the experiment a C12/14 fatty alcohol ethoxylate (C12 content 70-75%, C14 content 25-30%, molecular weight 238) with 2 mol of ethylene oxide (molecular weight 282, APHA number=10) was applied uniformly to the tube surface through a distributor slit in an amount of 21 kg/h (mass flow meter) (=0.077 kmol/h of fatty alcohol ethoxylate) at a temperature of 40° C. The cooling water feed temperature on the cooling mantle was adjusted to 15° C. The dilute SO3 was produced by combustion of sulfur to SO2 and subsequent oxidation to SO3. Using a feed tube, 0.98 kmol/h of dilute SO3 gas was introduced into the tubular reaction chamber at a concentration of 3.420 volume %, into which was incorporated an inserted tube of 0.75 inch (19.05 mm) inside diameter, a wall thickness of 0.5 mm and length of 300 mm. At the end of the reactor, the sulfo acid was degassed through a cyclone over a distance of approximately 10 m.Temperature measurements in the reaction chamber showed that a temperature maximum of 120° C. occurred at 400 mm from the fatty alcohol ethoxylate feed. The exit temperature at the end of the reaction tube was 35° C. The degassed sulfo acid removed continuously from the reactor was neutralized with sodium hydroxide (18 weight %), demineralized water, and sodium carbonate as buffer in a special dynamic mixer in such a way that a 70% paste was produced. The product has the following data:; After 4 weeks of running, the reactor was opened. No crusting was observed at the reactor head directly where the liquid raw material and SO3 meet. The color of the product during running production was not worsening either. The installation could have been operated further without any adverse influence on the quality.
References:
THE CHEMITHON CORPORATION US2008/306295, 2008, A1 Location in patent:Page/Page column 4-5; 7; Sheet 2; Sheet 4; Sheet 5; Sheet 6

3055-93-4
64 suppliers
$431.00/5g

56049-79-7
7 suppliers
inquiry

13150-00-0
18 suppliers
inquiry
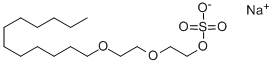
3088-31-1
44 suppliers
inquiry

143-15-7
442 suppliers
$5.00/25g
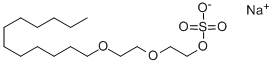
3088-31-1
44 suppliers
inquiry