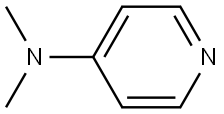
4-Dimethylaminopyridine synthesis
- Product Name:4-Dimethylaminopyridine
- CAS Number:1122-58-3
- Molecular formula:C7H10N2
- Molecular Weight:122.17
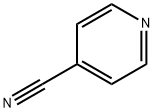
100-48-1
514 suppliers
$8.00/25g
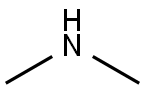
124-40-3
536 suppliers
$18.00/100ml
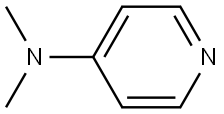
1122-58-3
1104 suppliers
$6.00/1g
Yield:1122-58-3 99.4%
Reaction Conditions:
Stage #1: pyridine-4-carbonitrilewith hydrogenchloride;acrylic acid at 90; for 1.5 h;Inert atmosphere;
Stage #2: dimethyl amine at 70; for 2.5 h;Inert atmosphere;
Stage #3: with sodium hydroxide at 70 - 90; for 3.5 h;Inert atmosphere;Temperature;Reagent/catalyst;
Steps:
1-5 Example 3
1) In a jet loop reactor based on the Venturi effect,Its operating principle is based on the Venturi effect, the loop operation is downward flow,And the end of the jet mixer 1 of the reactor is immersed in the liquid phase of the loop reactor,First perform nitrogen replacement, and then sequentially add 12 mol of acrylic acid and 10 mol of 4-cyanopyridine through the material feed port 5.Turn on the external circulation pump 3 at 90°C for high-speed jet mixing.2) Control the temperature at 90°C, and slowly add 13 mol of the hydrogen chloride raw material into the jet loop reactor through the gas raw material feed port 6.Through the jet mixer 1 spray mixing and realize the full reaction between the materials, the feeding time is 1.5 hours,After the feeding is completed, the reaction in the jet loop reactor continues for 1.5 hours, and the first step of the reaction is completed;3) After the first step of the reaction is completed, the temperature of the system is reduced to 70°C through the external heat exchanger 2.Slowly add 13 mol of the dimethylamine raw material into the injection loop reactor through the feed port 6, and realize the full reaction between the materials through the injection mixing by the injection mixer 1.The feeding time is 1.5 hours, after the feeding is finished,After the jet loop reactor continues to react for 1 hour, the second step of the reaction ends; 4) After the second step of the reaction is finished, control the temperature at 70°C, and add the liquid caustic soda raw material (mass concentration 40%, sodium hydroxide amount 45mol) into the reaction system through the material inlet 5, and the feeding time is 1.5 hours. After the feeding is completed, the heat is exchanged through the external heat exchanger 2, and the reaction of the control system continues at 90°C for 2 hours, and the third step of the reaction ends;5) After the reaction in the third step, stop the external circulation pump 3. The reaction liquid was transferred to the extraction kettle while it was hot. Toluene was added for extraction. The extraction temperature is 90°C.6) The organic phase obtained by extraction is added to activated carbon for decolorization and filtration, and white crystals are precipitated by cooling to obtain the product 4-dimethylaminopyridine.7) For the raffinate phase obtained by extraction, add hydrochloric acid to adjust the pH to 6. At a temperature of 95°C, add the next batch of raw material 4-cyanopyridine 10mol for extraction and recovery. The extracted organic phase directly passes through the material inlet 5 Put it into the jet loop reactor, add 0.2 mol of acrylic acid, turn on the external circulation pump 3 at 90°C for high-speed jet mixing. Start the next batch of reactions.Through the above reaction, 4-dimethylaminopyridine can be obtained as a white solid product. Statistics show that the recovery rate of acrylic acid in the process is 98%, the yield of 4-dimethylaminopyridine based on 4-cyanopyridine is 99.4%, and the content of 4-dimethylaminopyridine is 99.7%.
References:
CN111320572,2020,A Location in patent:Paragraph 0028-0058
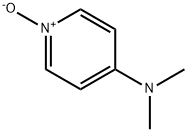
1005-31-8
68 suppliers
$52.00/250mg
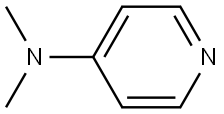
1122-58-3
1104 suppliers
$6.00/1g
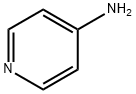
504-24-5
487 suppliers
$10.00/1g
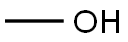
67-56-1
776 suppliers
$9.00/25ml
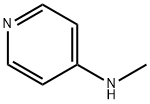
1121-58-0
186 suppliers
$20.00/1g
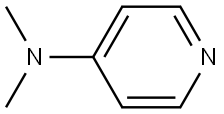
1122-58-3
1104 suppliers
$6.00/1g
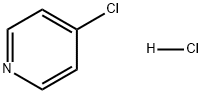
7379-35-3
437 suppliers
$5.00/1g
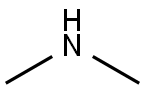
124-40-3
536 suppliers
$18.00/100ml
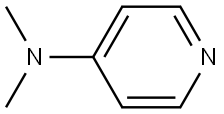
1122-58-3
1104 suppliers
$6.00/1g